Shellback pump problems can be addressed by identifying the root cause and implementing appropriate solutions. We will explore common issues associated with Shellback pumps, including leaks, motor failures, and reduced performance.
By understanding these problems and their underlying causes, you can effectively troubleshoot and resolve pump issues, ensuring optimal pump functionality and reliability. We will also provide some tips and recommendations for preventive maintenance to help minimize the occurrence of pump problems.
So, let’s dive in and learn how to tackle Shellback pump problems head-on.
Common Issues With Shellback Pumps
Shellback pumps are known for their reliability and excellent performance, but like any mechanical system, they can encounter problems over time. One common issue faced by Shellback pumps is leaking shaft seals. The shaft seals are designed to prevent fluid from leaking out of the pump, but wear and tear can cause them to become damaged or worn out, leading to leakage. Another problem that pump owners may experience is corroded impellers. Impellers are responsible for generating the pumping action, but exposure to corrosive fluids or inadequate maintenance can result in corrosion, hampering their effectiveness. Additionally, motor failure can occur due to various reasons such as overheating or electrical problems. It is essential to regularly maintain and inspect Shellback pumps to identify and address these issues promptly.
Understanding The Causes
Insufficient lubrication, contaminated fluid, and incorrect installation are common causes of pump problems in Shellback systems.
Insufficient lubrication can lead to increased friction between the moving components of the pump, resulting in excessive wear and decreased efficiency. It is important to regularly check and maintain the lubrication levels to ensure proper functioning of the pump.
Contaminated fluid can cause blockages and damage to the pump. Foreign particles, such as dirt or debris, can enter the system and obstruct the flow, leading to reduced performance or even complete failure. Regularly monitoring and filtering the fluid can help prevent these issues.
Incorrect installation can have a significant impact on pump operation. Improper alignment or connection of the pump can cause strain on the system and lead to poor performance. It is crucial to follow the manufacturer’s guidelines and consult experts if needed to ensure proper installation of the pump.
Troubleshooting Techniques
When troubleshooting Shellback pump problems, it is important to check for leaks and seal damage. Leaks can occur in various parts of the pump, including the seals, gaskets, and connections. Inspecting the pump for any signs of leakage and ensuring that all seals are in good condition is crucial for optimal performance.
Another area to assess is the impeller condition. A worn or damaged impeller can lead to poor pump performance and reduced efficiency. Check for any signs of wear, such as pitting or bent blades, and replace the impeller if necessary.
Additionally, it is important to evaluate the motor performance. Ensure that the motor is operating at the correct speed and that it is not overheating. A faulty motor can significantly affect the pump’s performance and lead to various issues.
In conclusion, properly troubleshooting Shellback pump problems involves checking for leaks and seal damage, inspecting the impeller condition, and assessing the motor performance. By addressing these key areas, you can effectively identify and resolve any pump-related issues.
Resolving Seal Problems
Shellback Pump Problems
Resolving Seal Problems
Seal problems can be a major issue for shellback pumps, leading to leaks and decreased efficiency. One common solution is to replace worn seals. When a seal becomes worn, it can no longer provide an effective barrier between the pump and the fluid it is moving. Replacing the worn seals with new ones can help restore the pump’s performance. However, it is important to follow proper seal installation techniques to ensure a proper and secure fit. This includes cleaning the seal area thoroughly and applying an appropriate lubricant. Another important factor is using high-quality seal materials. Investing in seals made from durable and resistant materials can significantly improve their longevity and performance.
Addressing Impeller Corrosion
Addressing Impeller Corrosion
- Identifying corrosive agents: To effectively address impeller corrosion, it is crucial to first identify the corrosive agents present in the pump system. This can be done by conducting regular inspections and analyzing the fluid being pumped for any corrosive properties.
- Employing protective coatings: Once the corrosive agents are identified, it is essential to employ protective coatings on the impeller. These coatings act as a barrier between the corrosive agents and the impeller surface, preventing corrosion.
- Regular impeller maintenance: Regular maintenance of the impeller is vital in preventing and addressing corrosion. This includes cleaning, lubricating, and inspecting the impeller for any signs of corrosion or damage. Additionally, replacing the impeller when necessary is crucial to maintain the pump’s performance and longevity.
Dealing With Motor Failure
Motor failure in shellback pumps can be a frustrating problem, but there are steps you can take to evaluate and address the issue. One important aspect to consider is the electrical connections. Ensure that all connections are secure, tight, and free from corrosion or damage. Loose connections can cause overheating and lead to motor failure.
To identify potential problems, it is crucial to conduct testing on various motor components. Check the windings, capacitors, and relays for any signs of damage or wear. Test the voltage and current to gauge the performance and efficiency of the motor.
If the motor is beyond repair, it may be necessary to consider a replacement. Evaluate the cost of repairs versus the cost of a new motor. Consider the age and condition of the pump as well, as it may be more cost-effective to invest in a new unit rather than prolonging the life of an older one.
By taking a systematic approach towards motor failure in shellback pumps, you can effectively diagnose the issue and determine the best course of action to ensure optimal performance and longevity.
Preventive Measures And Maintenance Tips
Regularly lubricating the pump components is an essential preventive measure to ensure the smooth functioning of Shellback pumps. By applying lubrication at recommended intervals, you can significantly reduce the risk of pump problems and extend the lifespan of the pump. Additionally, implementing fluid filtration systems can help to maintain the quality of the fluid being pumped and prevent contaminants from causing damage to the pump. These filtration systems can effectively remove impurities and particles, ensuring that the pump operates optimally. It is also important to follow proper installation guidelines when setting up the pump. Following the manufacturer’s instructions and guidelines can help prevent installation errors that may lead to pump problems. By adhering to these preventive measures and maintenance tips, you can effectively address pump issues and maximize the performance and longevity of your Shellback pump.
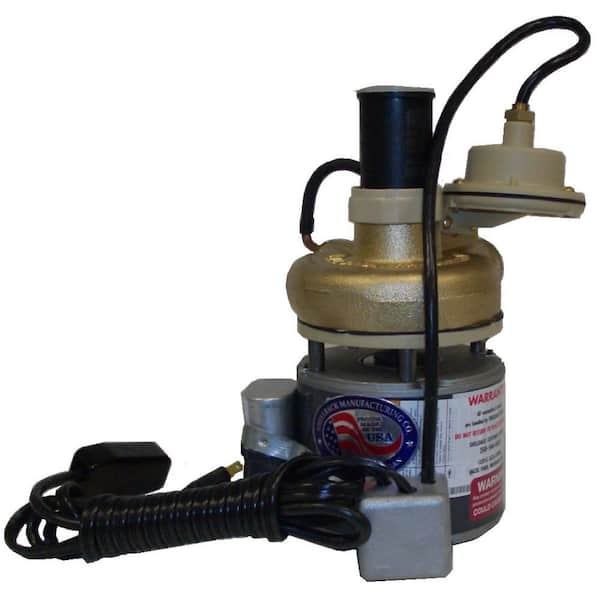
Credit: www.homedepot.com
Frequently Asked Questions Of Shellback Pump Problems
Why Does My Utility Pump Keep Shutting Off?
Your utility pump may be shutting off due to a clogged intake valve, a malfunctioning float switch, or a motor overload. Check for blockages, ensure the float switch is functioning properly, and verify the motor is not overheating. Fixing these issues should resolve the problem.
Why Is My Sump Pump Not Pushing Water Out?
Your sump pump might not be pushing water out due to a blocked discharge pipe, insufficient power supply, broken or clogged impeller, or a faulty float switch. Check for these issues and contact a professional if needed to fix the problem and ensure proper functioning of your sump pump.
Why Is My Utility Pump Not Working?
A utility pump may not be working due to a power issue, a blocked or damaged inlet pipe, a broken impeller or motor, or a malfunctioning switch. Check the power source, clear any obstructions, inspect the pump components, and test the switch to troubleshoot the problem.
Why Is My Sump Pump Not Pumping Fast Enough?
Your sump pump may not be pumping fast enough due to a clogged discharge pipe or a malfunctioning float switch. Check for any obstructions in the pipe and ensure that the float switch is functioning properly.
Conclusion
Dealing with shellback pump problems can be a challenging task. From troubleshooting and maintenance to replacement, it requires careful attention to detail. By understanding the common issues and their causes, you can take proactive measures to prevent breakdowns and ensure the smooth functioning of your pump.
Regular inspection, proper cleaning, and prompt repairs are key to extending the lifespan of your shellback pump and avoiding costly downtime. Remember, a well-maintained pump leads to efficient operations and increased productivity.